Batching or Blending 
Application Overview:
Many operations require combining liquids or gases. Batching or blending can be required for purposes of dilution, adding catalysts, chemical injection and establishing proper chemical formulas for stoichiometric balance. Continuous and On-Demand processing requires dependable design for product consistency and repeatability. Operator involvement can be time-consuming, costly, and a source of non-repeatability.
For example: Dilution of concentrated sulfuric acid in the production of Erythromycin and its by-products is completed in a two-stage process. The various diluted concentrations of sulfuric acid must be maintained within 3% to be used in multiple production processes.
Kates Solution:
Kates Flow Controllers with an accuracy of 1 ½% of SetPoint and quick 1-2 second response time to changes in upstream or downstream pressure surges make it an excellent choice to control the mix of products. Kates can also be actuated for remote positioning from a control room. Whether batching or blending, the time period a Kates is operating at its set flow rate is a direct indication of the volume of delivered product to the process.
In the Sulfuric acid dilution example above, a PVC Kates was used to meter the concentrated acid from an outdoor storage tank to the primary dilution tank. The initial and secondary dilution steps were accomplished by two Stainless Steel Kates units controlling the flow of water for the desired diluted concentrations. Incorporating the multiple Kates units eliminated the need for an operator to monitor the dilution process using control valves and rotameters.
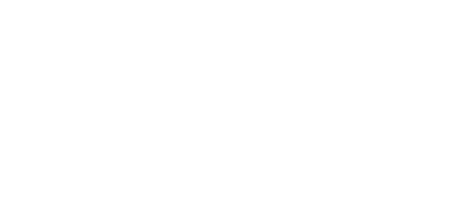
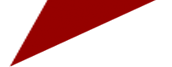
