How CVC Provides Customers with Innovative and Efficient Solutions
CVC contributes to customers’ growth objectives through collaborative processes which assist them to realize new products and market expansions. CVC prides itself on putting people first and providing superior engineering and manufacturing services within the development of their products!
Custom Valve Concepts has developed products for all major industries worldwide by combining fluid dynamics expertise with manufacturing excellence to yield quick development of exceptional products and components with reduced costs and highly successful initial designs. CVC takes a very proactive and independent approach to solving design challenges for new applications.
Defining Parameters
The first step in any custom development process is to fully define the parameters. This starts with understanding the applications’ demands such as temperature range, pressure range, and flow rates. Understanding what has been successful and unsuccessful in the past is key to design the proper solution. We are able to leverage CVC’s long history of application knowledge in order to know what kind of products exist and what works in various situations. In defining the parameters, we need to understand what is most important to the customer and their application, i.e. response time, longevity, etc. This gives us the ability to weigh these criteria in a matrix when analyzing design options.
Once we have defined the parameters, we move into a proof-of-concept stage. This is typically done through Computer aid design (CAD) in addition to manual calculations.
Research & Development
The Research & Development (R&D) processes at CVC have become more efficient and innovative over the years. From our engineering to manufacturing processes, CVC has created systems that mitigate R&D steps while efficiently assessing the products and tooling we currently produce or use.
The changes that have been made to the engineering process have improved the ability to determine the functionality and actions of products via Finite Element Analysis (FEA) and Computational Fluid Dynamic (CFD) methodologies. CVC then utilizes real-world field data from customers to simulate and evaluate responses to the applicable loading and stresses. The utilization of this FEA and CFD application and optimization process creates a system of analysis-led design of a product which helps reduce the testing and prototyping R&D steps of design optimization.
The manufacturing process has also been modified to create a more efficient manufacturing process via Computer-Aided Manufacturing (CAM).
For example, Kinematic responses within a system can be generated to determine close to accurate assumptions of machinery interaction through the duration of the machining operation. These simulations allow for manufacturing engineers to determine how the system will operate in terms of tooling clearances, feed and speed parameters, and any other potential collisions or mishaps within different industries’ particular machining operations. With this method in place, manufacturing engineers can begin machining with the assumption that operation parameters are known.
Once the proof-of-concept phase is complete, we move into prototyping and testing. The is an iterative process in which theories and design are validated and refined until an acceptable product is created. This could take a matter of days to years, depending on the size and complexity of the project.
Having the entire scope of sales, engineering, manufacturing, assembly, and testing all in one building allows us to streamline the prototype and testing process. Our engineers are able to interact directly with the valve technicians and machinists.
Once a product is finalized, the work is not over. We continually analyze results and refine designs in order to keep up with the latest technology.
With these processes and technologies in place, CVC has been able to streamline Lifecycle Management to produce a more effective engineering and manufacturing process.
Our Customers Are Our #1 Priority
Our commitment to our customers is to continue providing support for our products for a lifetime. As such, these methods are not only utilized for new designs but also for legacy models with an objective to improve the design and life of the product. For example, an existing valve technology used within the fracking industry was revised via our new R&D streamlined design, manufacture, and testing process. With parameter changes sent from the customer, the objective was to meet the customer’s new requirements but also increase the longevity of its preceding design. The valve was successfully redesigned, manufactured, and tested within six weeks, decreasing the R&D process by a great margin. Small, medium or large-scale projects; CVC’s prototyping capabilities allow us to provide quicker and more efficient product results. We have successfully designed over 450 products into process industries in the last 25 years. These types of products include flow controllers, high-speed solenoid valves, vacuum control valves, ratio blending valves, spray nozzles, check valves, and more!
With the continual improvement of processes through technology innovation and training, CVC will continue with its 75-year tradition of product innovation and expanding markets.
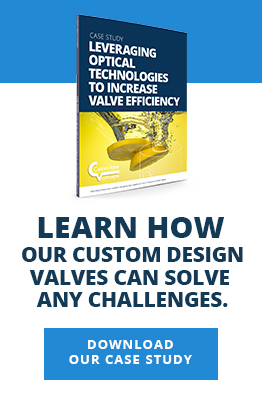
Sign up to receive the CVC Engineering Insights in Your Inbox:
Join us on Social Media!





Learn more about Custom Valve Concepts
Blog categories
- mechanical design (7)
- General (15)
- history (1)
- quality (4)
- manufacturing (4)
- meet the team (4)
- FAQ Kates (3)